If electrification of the vehicle fleet continues, this will mean lower CO2 emissions during operation. Alongside this fact, the focus is now turning to reducing the carbon footprint during production. And vehicle construction does indeed offer considerable potential for greater climate friendliness. The key words are durability, modularity and circular economy.
Electric vehicles, preferably fueled with "green" electricity, reduce emissions of climate-damaging (exhaust) gases during operation. Conversely, however, looking at the entire life cycle of this type of vehicle, the proportion of the "CO2 rucksack" from the manufacture of the vehicle is increasing. There are still major improvements to be made here, and these will not only help to limit emissions, but also offer economic advantages.
Long-lasting components capable of being used beyond the life cycle of the individual vehicle are the most important step in this direction. Other conditions, however, must also be met. One of these is modularity, which enables the simple replacement of components or complete modules. The other is a functioning concept for circular economy, in which parts are tested, conditioned, and fed into a resource-saving recycling system.
Feasibility project
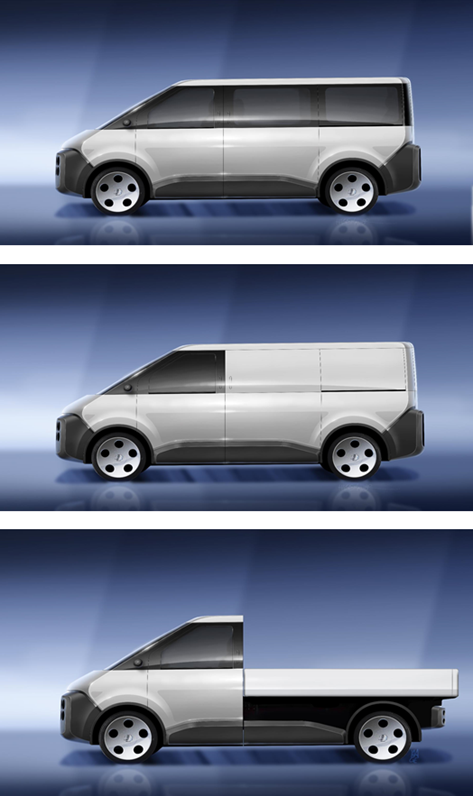
The KOSEL project has demonstrated that such a procedure is actually feasible. KOSEL stands for "Kreislaufgerechter Open-Source-Baukasten für elektrisch angetriebene Poolfahrzeuge" [recycling-oriented open source kit for electric pool vehicles]. The Fraunhofer Institute for Machine Tools and Forming Technology (IWU), the EDAG Group, Dresden University of Technology, Röchling Industrial SE, INVENT GmbH, the Emden-Leer University of Applied Sciences and BSMRG GmbH were involved in the project, the latter being a car sharing company which, with its "Carl and Carla" brand,operates using only minibuses and transporters in the 3.5 t class. The construction of such vehicles was therefore examined in greater detail in the course of the project.
As the name of the project suggests, an open source modular design is an elementary part of the concept. This means that there are defined interfaces between the individual modules, the front end, for example, or the battery box and rear end, and also with the superstructure. The modular principle enables the manufacturer to provide different external forms on a single platform – not just during production, but also when retrofitting the vehicle, meaning, for example, that a minibus, enclosed transporter or open flatbed truck can be built. As it is an open concept, providers of retrofit and conversion solutions are also able to access to the interfaces, and add their own individual solutions.
Durability is a must
If the modular system is to be not just open source, but also recycling-oriented, this calls for a set of components and modules capable of being used more than once – ideally beyond the life cycle of the individual vehicle. Instead of using metal carriers which are susceptible to corrosion, the consortium therefore opted for carbon fibre reinforced polymers CFRP). Although these have a comparatively high CO2 footprint in production, they can, if used correctly, compensate for this with their low mass and, in particular, their high fatigue strength over correspondingly long periods of repeated use.
This composite material is used, for instance, in EDaxle::LCV, the innovative semi-independent suspension with a transverse leaf spring developed by EDAG. The basic design consists of the transverse leaf spring acting on the axle beam via a lever arm. This concept allows the design of the rear end to be particularly flat, resulting in a low loading sill and level floor. This means that three standard pallets can be transported without restrictions. Great flexibility results from the possibility of changing the leverage ratios, so spring rates can be set for specific applications.
In order to guarantee operational safety during long-term use, INVENT developed a way of permanently monitoring this critical component. A network of piezoceramics monitors any material strains that occur. If small, invisible cracks appear in the material, they are detected as electrical voltage spikes. In the absence of such cracks, the component can continue to be used, with no need to replace it as a precautionary measure.
To guarantee the recyclability of components and parts, their durability must already be taken into account during the development phase – and this concerns not just the choice of material, but also a design which is open to future technological developments. In the present concept, one example of this can be found the areas in the front and rear ends which can be equipped with functional units and have been designed to enable the cameras and radar sensors needed for autonomous driving functions to be fitted. When retrofitting, there is therefore no call for the modification of the entire assembly.
Performance in crash scenarios
Protecting occupants from accidents is one of the key design criteria for all vehicles on public roads. To this end, a large number of crash scenarios including the side pole crash test are simulated and tested. Use was made of crash absorbers based on tubes made of carbon fibre reinforced plastic (CFRP) in this concept. These were installed in the rocker panel designed by Fraunhofer IWU and Röchling Industrial SE.
The effectiveness of the crash protection concept was validated by EDAG in simulations using the finite element method. The results show that there is little intrusion into the vehicle at both 90° (C1) and 75° (C2). At the same time, the desired slightly progressive course of the counterforce generated becomes apparent. An impact in the edge region (C3) also leads to the expected behavior.
A comparison of environmental impacts
The aim of the concept is to reduce the impact the vehicle has on the environment. In an examination covering three vehicle life cycles in the course of 30 years, the Chair of Energy Economics at the Dresden University of Technology was able to show that significant advantages result if the product life cycle of individual components is extended over several vehicle generations. The comparison dealt both with the different concepts and with the possibility of recycling. Please note that not all material combinations provide the required service life.
The results speak for themselves: The analysis of the modular system shows a reduction of more than 60 %, in particular as a result of recycling. This shows a distinct advantage for the environment, which can only be realized through circular economy.
The modular platform KOSEL, in conjunction with the zone-based EE architecture developed in the research project ZOBAS, was awarded the Sustainability Award in Automotive by the ATZ.
Do you have questions on reducing the carbon footprint in production, on concepts such as modularization in vehicle construction, or on the installation of a circular economy? Then contact Dr. Stefan Caba, Head of the Innovations Field Sustainable Vehicle Development at EDAG. Or download our white paper "Climate-Friendly Circular Economy in Vehicle Construction", which contains additional details and findings from the KOSEL project.