Wenn die Fahrzeugflotte immer weiter elektrifiziert wird, bedeutet das einen geringeren CO2-Ausstoß im laufenden Betrieb. Dafür rückt nun der „Carbon Footprint“ der Produktion stärker in den Fokus. Tatsächlich bietet der Fahrzeugbau noch erhebliche Potenziale zu mehr Klimafreundlichkeit. Die Stichworte heißen Langlebigkeit, Modularität und Kreislaufwirtschaft.
Elektrische Fahrzeuge, die bevorzugt mit „grünem“ Strom betankt werden, senken den Ausstoß klimaschädlicher (Ab-)Gase im laufenden Betrieb. Blickt man auf den gesamten Lebenszyklus eines solchen Fahrzeugs, nimmt im Gegenzug der Anteil des „CO2-Rucksacks“ aus der Herstellung des Fahrzeugs zu. Hier lassen sich noch erhebliche Verbesserungen erreichen, die nicht nur einen Beitrag zur Begrenzung der Emissionen leisten, sondern auch wirtschaftliche Vorteile bieten.
Langlebige Komponenten, die sogar über den Lebenszyklus des einzelnen Fahrzeugs hinaus genutzt werden können sind der wichtigste Schritt auf diesem Weg. Dazu bedarf es allerdings weiterer Voraussetzungen. Die eine ist Modularität, die einen einfachen Austausch von Bauteilen oder ganzen Baugruppen ermöglicht. Die andere ist ein funktionierendes Konzept für eine Kreislaufwirtschaft, in der Teile geprüft, aufbereitet und einer ressourcenschonenden Wiederverwendung zugeführt werden.
Projekt zur Machbarkeit
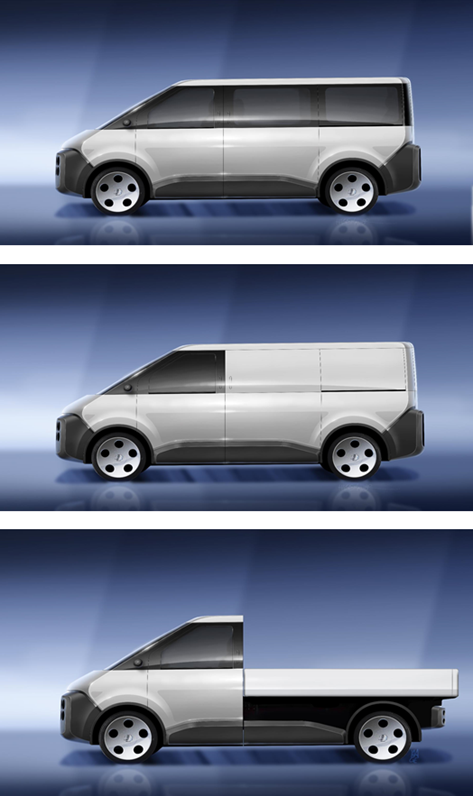
Dass ein solches Vorgehen tatsächlich umsetzbar ist, hat das Projekt KOSEL dargelegt. „KOSEL“ steht für“ Kreislaufgerechter Open-Source-Baukasten für elektrisch angetriebene Poolfahrzeuge“. Beteiligt waren das Fraunhofer Institut für Werkzeugmaschinen und Umformtechnik (IWU), die EDAG-Group, TU Dresden, Röchling Industrial SE, INVENT GmbH, Hochschule Emden-Leer sowie BSMRG GmbH. Letzterer ist ein Carsharing-Betreiber, der unter der Marke „Carl und Carla“ Kleinbusse und Transporter der 3,5t-Klasse anbietet. Im Rahmen des Projektes wurde daher der Bau solcher Fahrzeuge näher untersucht.
Wie der Name des Projektes bereits verrät, ist eine Open-Source-Modulbauweise elementarer Teil des Konzeptes. Das bedeutet, dass zwischen den einzelnen Modulen, wie etwa Vorderwagen, Batteriekasten und Hinterwagen, definierte Schnittstellen existieren, ebenso zu den Aufbauten. Das Baukastenprinzip ermöglicht es dem Hersteller, auf einer Plattform unterschiedlichen Außenformen zu realisieren – nicht nur bei der Produktion, sondern auch beim „Retrofit“ des Fahrzeugs. So kann beispielsweise sowohl ein Kleinbus als auch ein geschlossener Transporter oder ein offener Pritschenwagen gebaut werden. Als offenes Konzept steht der Zugang zu den Schnittstellen auch Anbietern von Nach- und Umrüstlösungen offen, die zusätzliche individuelle Lösungen darauf aufsetzen können.
Langlebigkeit ist Pflicht
Dass der Baukasten nicht nur „Open Source“, sondern auch kreislaufgerecht ist, bedingt ein Set von Bauteilen und Modulen, die mehr als einmal verwendbar sind – im Idealfall über den Lebenszyklus des einzelnen Fahrzeugs hinaus. Statt auf korrosionsgefährdete Metallträger setzte das Konsortium daher auf kohlenstofffaserverstärkte Kunststoffe (CFK). Diese weisen zwar einen vergleichsweise hohen CO2-Fußabdruck in der Herstellung auf, können diesen aber bei richtigem Einsatz über die geringe Masse und insbesondere die hohe Dauerfestigkeit bei entsprechend langer und mehrmaliger Nutzung ausgleichen.
Der Verbundwerkstoff kommt beispielsweise bei der von EDAG entwickelten innovativen Koppellenkerachse mit Querblattfeder EDaxle::LCV zum Einsatz. Das Grunddesign besteht aus einer Querblattfeder, die über einen Hebelarm auf den Achskörper wirkt. Dieses Konzept ermöglicht einen besonders flachen Aufbau des Hecks, sodass eine niedrige Ladekante und ein ebener Boden entstehen. Drei Standardpaletten können so ohne Einschränkungen transportiert werden. Besondere Flexibilität ergibt sich hierbei aus der Möglichkeit, die Hebelverhältnisse zu ändern. So können Federraten gezielt auf den Anwendungsfall eingestellt werden.
Um auch bei einem langfristigen Einsatz die Betriebssicherheit zu gewährleisten, hat INVENT eine dauerhafte Überwachung dieses kritischen Bauteils entwickelt. Ein Netzwerk aus Piezokeramiken registriert auftretende Materialdehnungen. Treten kleine, nicht sichtbare Risse im Werkstoff auf, werden diese in Form elektrischer Spannungsspitzen erfasst. Bleiben sie dagegen aus, kann die Komponente weiterverwendet werden und muss nicht vorsorglich ersetzt werden.
Um eine Wiederverwertbarkeit von Teilen und Komponenten zu gewährleisten, muss die Langlebigkeit bereits in der Entwicklung mitgedacht werden – und das bezieht sich nicht nur auf die Materialauswahl, sondern auch in einem Design, das offen ist für künftige technologische Entwicklungen. So wurden im vorliegenden Konzept beispielsweise die mit Funktionseinheiten bestückbare Bereiche in Front und Heck so ausgelegt, dass Kameras und Radarsensoren angebracht werden können, die für Funktionen des autonomen Fahrens erforderlich sind. Bei einer Nachrüstung sind daher keine Änderung der gesamten Baugruppe erforderlich.
Verhalten in Crashszenarien
Für alle Fahrzeuge, die im öffentlichen Straßenverkehr unterwegs sind, stellt der Schutz der Insassen vor Unfällen ein wesentliches Auslegungskriterium dar. Hierzu wird eine Vielzahl von Crashszenarien simuliert und getestet, darunter der sogenannte seitliche Pfahlaufprall. Im vorliegenden Konzept kamen Crashabsorber zum Einsatz, die auf Röhren aus kohlenstofffaserverstärktem Kunststoff basieren. Diese wurden im Schweller verbaut, der von Fraunhofer IWU sowie der Röchling Industrial SE konzipiert wurde.
Die Wirksamkeit des Crashschutzkonzepts wurde von EDAG in Simulationen nach Finite-Elemente-Methode validiert. Die Ergebnisse zeigen, dass sowohl in 90° (C1) als auch in 75° (C2) eine geringe Intrusion in das Fahrzeug stattfindet. Gleichzeitig zeigt sich der gewünschte leicht progressive Verlauf der erzeugten Gegenkraft. Auch ein Auftreffen im Randbereich (C3) führt zum erwarteten Verhalten.
Umweltauswirkungen im Vergleich
Das Ziel des Konzepts ist die Verringerung der Auswirkungen des Fahrzeugs auf die Umwelt. Der Lehrstuhl für Umweltökonomie der TU Dresden konnte hier in einer Betrachtung über drei Fahrzeuglebenszyklen in 30 Jahren zeigen, dass sich signifikante Vorteile ergeben, wenn der Produktlebenszyklus von einzelnen Komponenten über mehrere Fahrzeuggenerationen verlängert wird. Verglichen wurden sowohl unterschiedliche Materialauswahl, aber auch die Möglichkeit zur Kreislaufführung. Hierbei ist zu beachten, dass nicht alle Materialkombinationen die erforderliche Lebensdauer zulassen.
Das Ergebnis spricht für sich: Die auf den Baukasten bezogene Betrachtung zeigt eine Reduktion von über 60 Prozent, die sich insbesondere aus der Kreislaufführung ergibt. Es zeigt sich somit ein entscheidender Vorteil für die Umwelt, der sich nur über Kreislaufwirtschaft realisieren lässt.
Die modulare Plattform KOSEL wurde in Verbindung mit der im Forschungsprojekt ZOBAS entwickelten zonenbasierten EE-Architektur mit dem Sustainability Award in Automotive von der ATZ ausgezeichnet.
Haben Sie Fragen zur Verringerung des CO2-Fußabdrucks in der Produktion, zu Konzepten wie Modularisierung im Fahrzeugbau oder der Installation einer Kreislaufwirtschaft? Dann sprechen Sie mit Dr. Stefan Caba, Leiter Innovationsfeld Nachhaltige Fahrzeugentwicklung bei EDAG. Oder laden Sie sich unser Whitepaper „Klimafreundliche Kreislaufwirtschaft im Fahrzeugbau“ herunter, das weitere Details und Erkenntnisse aus dem Projekt KOSEL bereithält.